CONDUCTION HEAT ASSISTED FRICTION ELEMENT WELDING
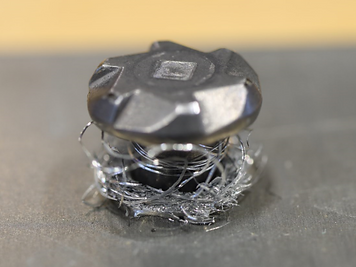
Poor weld with Chipping
Problem Statement: To reduce the formation of undesirable chips in Al 7075 - T6 to enable the use of this novel joining technique in automotive production lines.
Method:
-
Thermal Assistance to the Aluminum top sheet through conduction heating.
-
Full factor DoE with all process parameters to determine the cause of chipping.
-
Designing and drafting of a modified downholder with Geometric Dimensioning and Tolerancing using Solidworks.
-
Simulated the heat conduction in Ansys Workbench to find the desired top sheet temperature.
-
Rigorous experimentation to determine the repeatability of results.

Results:
-
The average chipping score increased from 2.2 to 4 (the higher the better).
-
The simulation model had an average percent error of 13% when compared against experimental results.
-
Submitted my findings as a research paper and presented the results in MSEC 2021 conference held during June 2021.
Good weld without Chipping
LASER ASSISTED FRICTION ELEMENT WELDING
The conduction FEW had the disadvantage of increased process time. The time to heat the downholder, the time of contact with the aluminum workpiece, and the actual process all added to about a total process time of 1 minute. To overcome this disadvantage, a rapid more localized method of heating was selected. Laser has the advantage of heating the workpiece locally at the contact of the friction element. The CO2 laser employed heated the aluminum workpiece locally at the desired spot in under 10 seconds. This time will be further reduced by using a higher power laser heater.
Submitted the findings as a research paper in the IMECE 2021 conference.

RESISTIVE HEATING FRICTION ELEMENT WELDING
The heating method explored herein was resistive heating achieved through electrical current. A clear distinction must be made between the present method and a concept known as electrically assisted manufacturing (EAM). EAM is typically performed by passing an electric current through the workpiece during processing. This method differs in that the electric current is turned off before the process is performed. EAM has also been used to describe processes in which materials were altered prior to processing using electric currents. This has mainly been achieved through high current pulses.
Submitted the findings as a research paper in the IMECE 2021 conference.
